

☆☆☆Web配信セミナー☆☆☆
『開発におけるフレームワーク有効活用』
〜製品開発プロセスの時間短縮,論理的業務推進〜
S250729AW

☆☆☆本セミナーは、Zoomを使用して、行います。☆☆☆
開催日時:2025年10月7日(火)10:30-16:30
受 講 料:お1人様受講の場合 53,900円[税込]/1名
1口でお申込の場合 66,000円[税込]/1口(3名まで受講可能)
★本セミナーの受講にあたっての推奨環境は「Zoom」に依存しますので、ご自分の環境が対応しているか、
お申込み前にZoomのテストミーティング(http://zoom.us/test)にアクセスできることをご確認下さい。
★インターネット経由でのライブ中継ため、回線状態などにより、画像や音声が乱れる場合があります。
講義の中断、さらには、再接続後の再開もありますが、予めご了承ください。
★受講中の録音・撮影、スクリーンキャプチャ等は固くお断りいたします。
…関連講座…【究極の設計 防水機構設計とそのフロントローディングプロセス講座】
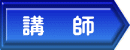
平池 学(ひらいけまなぶ) 氏
神上コーポレーション株式会社 顧問 / 構造アナリスト
<講師紹介> |
元 株式会社テクノプロ テクノプロデザイン社 札幌サテライト代表技術者 / 元 日本ピーマック株式会社 技術部 主任
☆建築衛生設備(ビル用エアコン)から携帯電話,工場生産設備の設計を行っていた。特に携帯電話の設計についてはガラケー〜スマホ・タブレットの開発全般に関わり、その中で強度解析(CAE)について多くの知見を得た。
【神上コーポレーション】…IoT開発リスクへジャー 開発体制のリスク診断を実施しています(無料)。5ゲン主義に基づく設計&指導。材料から構造設計&指導(化学⇔機構の融合)。トータル製品開発の設計&指導。IoT、ウェアラブル端末機器設計エキスパート。 |
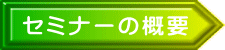
|
製品開発業務では様々な「迷い」「混乱」「困りごと」「無知」「認識不足」が起こり、私たち強いてはプロジェクトチームを苦しめます。自分だけでは解決不可能な「困りごと」もしばしばあります。仕事は、ひとりでやれるものではありません。多くの仲間が協力することで課題を解決し、次のステージへ進められるのです。そこで、「考え方を整理する(思考の強化)」「仕事の進め方を整理する(作業時間短縮)」「みんなで共通の目標を持って進める(共通認識の形成)」などのルールや手順を定めた「フレームワーク」が役立ちます。仕事の進め方が上手な人、経験を積んでいるベテランさんは、意識的/無意識関わらずフレームワークを有効に利用して、周囲との意思疎通を柔軟にし、開発をぐいぐい進めていきます。
今回、開発現場・製造現場に特化し、開発プロセスの流れに沿って主要なフレームワークと活用シーン例を一緒に確認し、業務に取り入れるヒントを探していきたいと思います。
みなさんの仕事の合理化・効率化に役立てれば幸いです。
|
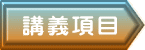
1 開発プロセス〜モノづくりの流れ〜
1.1 そもそも開発プロセスとは…全員が同じ方向へ!
1.2 意思決定の道筋を立てる…DRの重要性
1.3 問題の解決方法は1つじゃない!
1.4 新しいプロセスを使う…フロントローディング、デジタルツイン
1.5 既存の枠組み(フレームワーク)を利用してプロセス推進!
2 事業検討〜新しい製品・サービスの概念創造〜
2.1 ブレインストーミング…求められるモノとは
2.2 3C分析/4P分析…モノの価値,市場の要求を考える
2.3 Need/Wantマトリクス…市場の要求を見極める
3 商品企画〜新商品の企画検討〜
3.1 目標設定…終着点をハッキリと定める
3.2 ロードマップ…モノづくりの流れを共有する
3.3 As is / To be…現状と理想の差を確認する
3.4 スキーム図…図示化で共通の理解を高める
3.5 SCM…材料調達から販売までを最適化
4 構想〜実現の作業着手〜
4.1 QCD…モノの品質、値段、調達を意識する
4.2 三現主義/五ゲン主義…今までの課題を振り返る
4.3 SECIモデル…「個人の知」を「全体の知」に変え品質向上
4.4 FTA / FMEA…課題の対策手段と未然防止手段
4.5 意思決定マトリクス…アイデアを客観的に検証する
4.6 標準化/共通化/単純化…同じ部品,同じ構造で安定した品質へ
4.7 ユニット/プラットフォーム…同じ部品群でスピードと安定性を向上
4.8 PERT図…各ステージの日程を管理する
5 設計〜モノづくりの開始〜
5.1 QC7つ道具/新QC7つ道具…改善内容の把握手法
5.2 シックスシグマ@…設計精度を見極める
5.3 グラフ化@…情報を視覚化して理解を深める
5.4 パレート図…達成度を視覚的に認識・共有する
5.5 PLC…製品寿命に適した部品・加工か判断
5.6 PDM / BOM…情報管理を一元化して取りこぼし回避
6 試作〜モノを具体化する〜
6.1 シックスシグマA…出来上がったモノはどこが違うか
6.2 グラフ化A…課題を視覚化して認識・対策する
6.3 ロジックツリー…課題発生の経緯を深掘りする
6.4 関連図法…課題の因果関係を探る
6.5 なぜなぜ分析…課題の発生原因を追究する
6.6 系統図…目的と手段の関連性を明確化
6.7 マトリックス図法…要素同士の関連性を探る
6.8 ペイオフマトリクス…要求と難易度を整理して実現性を探る
6.9 PDCA…改善サイクルを継続して回し続ける
7 量産 / 製造〜マスプロダクトへの移行〜
7.1 特性要因図…量産の安定を阻害するものを探す
7.2 ヒストグラム…生産のバラツキ度合いを確認する
7.3 管理図…異常状態の原因を究明する
7.4 工程能力指数…モノの出来上がりを数値化して判断する
7.5 回帰分析…モノの出来上がりの傾向を知るでスピードと安定性を向上
8 開発後〜量産開始後にも必要なコト〜
8.1 4M変更…量産時のトラブル予防・対策・解消
8.2 KPT/YWT…業務の良い点・改善すべき点を振り返る
8.3 ノウハウ・ナレッジ…手にした知見を全員で共有する
8.4 業務の棚卸しと改善…業務内容を見える化して効率改善
9 プロセスを横断して使うフレームワーク〜普段から意識すること〜
9.1 5S…仕事のしやすい環境を維持する
9.2 ムリ・ムダ・ムラ…業務を停滞させる原因を探り排除する
9.3 ECRS〜業務内容の重要度を整理して削除する
9.4 ホウレンソウ・カクレンボウ…チーム運営の円滑化を目指して
9.5 5W1H…円滑なコミュニケーションのために
10 まとめ
10.1 枠組みを作るだけ・使うだけではダメ
10.2 何度も繰り返すことが必要
10.3 みんなで協力、みんなで実施
10.4 さらに仕事がやりやすくなるために
10.5 仕事の進め方の改善手段
10.6 1つの方法にとらわれない
10.7 考えているだけでは改善しない
10.8 みなが1つになること
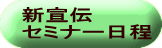