トリケップス文献調査用資料 CD-WS089
高密度表面実装(SMT)におけるLSIパッケージング技術
刊行月:1988年10月、価格:43,890円(税込)
体裁:CDR、216頁 監 修
西 邦彦 株式会社日立製作所 武蔵工場 パッケージ技術開発部 主任技師
執筆者
西 邦彦 株式会社日立製作所 武蔵工場 パッケージ技術開発部 主任技師
西田秀行 日本アイ・ビー・エム株式会社 野洲事業所 高密度実装基板生産技術 係長
崎元正教 株式会社日立製作所 武蔵工場 検査部 主任技師
閑野義則 沖電気工業株式会社 電子デバイス事業本部 パッケージ開発部 材料開発課
係長
戸塚憲男 沖電気工業株式会社 電子デバイス事業本部 パッケージ開発部 材料開発課
課長
南部正剛 沖電気工業株式会社 電子デバイス事業本部 パッケージ開発部 材料開発課
部長
福島二郎 三菱電機株式会社 北伊丹製作所 アセンブリ技術部 アセンブリ第2課 課長
黒柳 卓 古河アルミニウム工業株式会社 技術部
浦野孝志 日立化成工業株式会社 南結城工場 開発部 主任技師
畑田賢造 松下電器産業株式会社 半導体研究センター 半導体基礎研究所 主任技師
櫻井寿春 株式会社東芝 集積回路事業部 集積回路組立技術部 主務
藤田繁男 三菱電機株式会社 北伊丹製作所 アセンブリ技術部 第3課 主幹
笹本敏郎 日本電気株式会社 回路基板事業部 信頼性品質管理部 技術課 課長
|
第1章 LSIパッケージング技術の基礎
1 パッケージの種類
1.1 緒言
1.2 パッケージの種類と特徴
1.3 パッケージの標準化
2 パッケージング技術-パッケージの構造と製造プロセス-
2.1 ペレット付け
2.2 ワイヤボンディング
2.3 モールド
2.4 完成品リード処理
2.5 マーキング
3 パッケージの信頼性
3.1 信頼性とは
3.2 熱応力評価法
3.3 信頼性とその支配要因
4 実装上の問題
5 今後の課題
5.1 薄型化
5.2 多ピン化
第2章 SMT対応パッケージング技術
第1節 SMT対応ソルダリング技術
1 はじめに
2 フローソルダリング
2.1 フローソルダリングとは
2.2 噴流方式(Wave Soldering)
2.3 浸漬方式(Dip Soldering)
2.4 その他のステーション
3 リフローソルダリング
3.1 リフローソルダリングとは
3.2 加熱炉方式
3.3 気化潜熱方式(V.P.S.)
3.4 光束照射方式
4 その他の関連技術
4.1 フラックスとその選定
4.2 ソルダレジスト
4.3 はんだ材料
4.4 基板、パッケージの前処理
5 工程管理
6 接合寿命
6.1 熱膨張係数
6.2 はんだ付け接合部の機械的特性とサイクルひずみ
6.3 信頼性試験
7 おわりに
第2節 検査方法、評価方法
1 概要
2 検査方法
2.1 パッケージクラック検査方法
2.2 リード-レジン隙間検査方法
2.3 その他の検査法
3 評価方法
3.1 リフロークラック評価方法
3.2 寿命評価方法
第3節 はんだリフロー時におけるクラック発生メカニズム
1 パッケージクラックの発生メカニズム
2 パッケージ内水分濃度分布の評価法
3 リフロー時に発生する応力計算
第4節 クラック防止のための防湿策
1 はじめに
2 構造の検討
3 レジン材料の検討
4 防湿策
第5節 SMT対応パッケージング技術
1 概説
2 SMT対応パッケージングの種類
3 表面実装型および挿入実装型ICパッケージの基板実装方法の比較
4 ソルダリング工程における表面実装型ICの信頼性
5 ソルダリング工程を可能とするパッケージ技術
5.1 VKパッケージ
5.2 高密着性化
5.3 乾燥梱包
6 今後の動向
第6節 SMT対応パッケージング技術
1 SMT対応パッケージ(SMD)の現状
1.1 SMD開発の背景
1.2 SMDの現状と問題点
2 SMT対応パッケージング技術
2.1 モールド技術
2.2 外装処理技術(メッキ技術)およびリード加工技術と実装技術との関係について
2.3 実装技術
3 SMDパッケージの信頼性
第7節 リードフレーム材料とその特性
1 概要
2 パッケージとリードフレーム
2.1 リードフレームの役割
2.2 組み立て工程とリードフレーム
2.3 リードフレームの製造工程
2.4 パッケージの動向
3 リードフレーム材料の特性
3.1 1次特性と評価方法
3.2 成型性とsの評価方法
3.3 2次特性(実用性)とその評価方法
4 リードフレーム材料の開発動向
4.1 リードフレーム用Cu合金の分類
4.2 SMD用リードフレーム材料の開発動向
4.3 TAB技術とTABテープ
4.4 実装技術と金属ベース基板の開発
4.5 Fe系材料とCu系材料の比較
5 リードフレーム材料の今後の動向
第8節 モールド材料とその特性
1 概要
2 表面実装パッケージ(SMD)用モールド材料の設計
2.1 モールド材料の現状と問題点
2.2 対策方法とそのレベル
2.3 低応力化
3 各種モールド材料の特長と欠点
4 モールド材料からみた将来対応技術
5 まとめ
第3章 TAB技術
1 概要
2 TAB技術の構成
2.1 フィルムキャリアテープの構成
2.2 フィルムキャリアテープ材料
3 ILB技術
3.1 ILBの方式
3.2 バンプ形成技術
3.3 ボンディング技術
4 樹脂封止技術
5 OLB技術
6 今後の動向と展望
第4章 多ピン薄型化パッケージング技術
1 パッケージ多ピン化の動向
1.1 パッケージ多ピン化の限界
1.2 多ピン化対応パッケージ
2 多ピン薄型パッケージ
2.1 モールドタイプパッケージング技術
2.2 薄型パッケージング技術
3 今後の課題
第5章 ICカード用超薄型パッケージング技術
1 ICメモリカードの概要
2 ICメモリカード対応実装部品とその特徴
2.1 受動部品
2.2 能動部品
2.3 その他の部品
3 ICカード用超薄型パッケージング技術
3.1 超薄型パッケージの実例と今後の方向
3.2 超薄型パッケージの実装技術
4 ICメモリカード実装事例
第6章 モジュールのパッケージング技術
1 モジュール化の背景
2 セットメーカからみたICパッケージへの要請
2.1 ICパッケージの動き
2.2 面実装用パッケージの要求条件と特徴
3 各種モジュールのパッケージング技術
3.1 厚膜ICタイプ
3.2 COBタイプ
3.3 トランスファモールドタイプ(COMPACT)
4 日本電気㈱におけるSMDタイプの高密度パッケージの製品例
4.1 厚膜タイプ
4.2 COMPACTタイプ
5 今後のハイブリッドICの動向
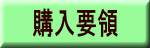
|